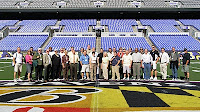
Synthetic turf installation and maintenance activities continue to generate increased interest by the park and recreation industry, customers, and users. National Park and Recreation Association held a synthetic turf workshop at their annual convention in Baltimore, MD, October 2008.
What is the true cost of these installations and the maintenance costs was a theme during this workshop held at the Baltimore Ravens football stadium on October 21, 2008. The workshop was hosted by Jeanette M. S. Tansey, Baltimore County Department of Recreation and Parks, with presenters including Jeffrey L. Bruce, President, Jeffrey L. Bruce & Company, LLC, a national landscape architectural firm, and Graham Hayes, CEO, Dedicated Operational Contracting, LLC.
Jeff Bruce covered some of the critical decisions in installing a new synthetic turf systems. There are four primary areas that a customer should ensure is part of the project,
1) hiring an engineer that is familiar with the soil types and synthetic turf installation in your area,
2) ensuring that an experience construction company with establishing a base for the turf carpet has been hired,
3) a reputable turf product has been selected for the environment and type of play expected, and
4) an experienced turf installer that has a reputation of not having to come back for repairs on seams.
The presenters emphasized that the Sports Turf Managers Association's Synthetic and Natural Turf Grass Guide as a valuable tool.
Graham Hayes stated that because many of these fields are installed between Memorial and Labor Day the crews on site experience tremendous schedule pressures. It is imperative to have a knowledgeable inspector on site to verify compliance with specifications, e.g, soil base is laser leveled, rock base meets particle size and depth and is packed, sand infield mixture with crumb rubber, trenches are properly filled and packed, amount and type of glue used, etc.
They re-emphasized that the synthetic turf fields are not maintenance free and require activities to maintain their warranty clauses.
Many of the existing turf problems are attributed to poor base construction, in appropriate infield material application and mixture, not maintaining the appropriate infield depth (turf fiber laying over thus wearing much quicker and being exposed to UV which degrades them), allowing problem seams becoming a big maintenance issue, etc.
It was highly recommended that during budgeting for a turf system that yearly maintenance be included, possibly a maintenance contractor visiting on-site at least yearly and be done in conjunction with the general contractor's annual site visit.
The workshop concluded with a walk-through of the facilities to include maintenance facilities, turf field, sky box, and press box.
At the time there was discussion on use of removable turf field paint products for multi-purpose fields. One concern is how quickly this would cause wear on the turf fibers from being manually or mechanically agitated after a removal agent is applied to help break down the paint quicker. Several members at the workshop noted that most of the removable paint products have a corresponding cleaning agent that properly matches up with the chemical properties of the paint formulation. The wear issue was not necessarily the primary issue, rather the ghosting effect from not being able to remove all the residual paint, especially when a infield material is used, is a bigger issue. More than one person mentioned that is better to under apply than over apply the turf field marking paint to reduce the ghosting effect.